What are the characteristics of vacuum casting?
Vacuum casting is one of the three main casting methods that can be used to pull the material into the mold. Vacuum casting has many advantages, many of which make it very suitable for ferrous and non-ferrous metals. The process usually involves drawing molten metal into the mold, which reduces turbulence and prevents scum and other impurities from entering the final casting.
Vacuum casting is usually related to a common variation of sand casting and can also be used with elastomers. Another name for worker vacuum casting is anti-gravity filling, because this usually involves pulling a material up into the mold, rather than pouring from the top. Since the material is not poured or forced in by air pressure, there is usually very little turbulence associated with this method. This can make the gate mechanism simpler than other types of castings, which may reduce overall costs. A simple gating mechanism can also increase the efficiency of the method, as less metal tends to solidify on it. This may result in an efficiency increase of 50% or more.
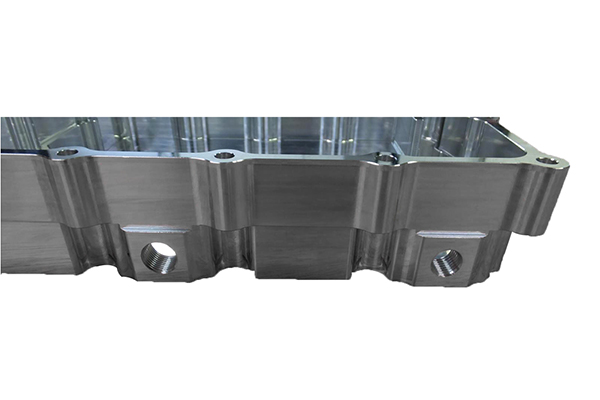
The molten metal will then come into contact with the sand, at which point it will take on the shape of the mold. When the vacuum is removed, the sand will release the solidified metal and the mold can be used again. If other methods cause air retention problems, vacuum casting of the elastomer can also be performed. This method usually uses a silicone mold placed in a vacuum chamber. Then, the liquid elastomer will be degassed before being introduced into the mold. The vacuum helps to ensure that the elastomer fills any details of the mold and reduces the possibility of any bubbles. After filling the mold, the vacuum can be eliminated and the workpiece can be further processed.